Kolbenfüller für die Fleischindustrie
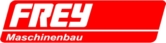
K-LINE KK500 Kontinuierlicher Kolbenfüller für die Industrie
K-Line arbeitet mit einem einzigartigen Kreiskolbensystem. 6 umlaufende Kolben fördern das Produkt vom Aufladen der Kolben bis zum groß-dimensionierten Deckelauslauf.
Das Frey Kolbenfördersystem ist das derzeit produktschonendste Förderprinzip. Schmiereffekte werden auf ein absolutes Minimum reduziert, dadurch können selbst kritische Produkte optimal gefüllt werden. Das Ergebnis ist ein herausragendes Füllbild, auch bei Verarbeitungstemperaturen über 0° C. Damit eignet sich der KK500 vor allem für Produzenten von Halb- und Dauerware, sowie Hersteller von luftgetrockneter Rohwurst.
Der K-Line KK500 erreicht eine Füllleistung von max. 8.500 kg/h und einen Fülldruck von bis zu 25 bar. Die Portionierleistung beträgt max. 350 Port./min.
KK500 eignet sich aber auch besonders für alle sensiblen Produkte und Ware mit stückigen Einlagen. Eine patentierte wechselbare Schneidkante sorgt für eine klare Trennung des Produkts bei der Befüllung der 500ml großen Füllkammern. Dadurch erreicht der KK500 eine sehr hohe Portioniergenauigkeit und ein Quetschen des Produkts wird verhindert.
Ein dem Brätfluss optimal angepasster Auslauf (Standard 65mm, optional bis zu 75mm Durchmesser) behandelt das Füllgut äußerst schonend. All diese Maßnahmen führen konsequent zu einem perfekten Endprodukt.
Die Vakuumfüller wurden auf der IFFA in HD Design vorgestellt. Dichtungen sind nun in der Hygienefarbe Blau und totraumfrei ausgeführt. Es wurden konstruktiv zusätzliche vorgelagerte Back Up Dichtungen hinzugefügt, die der Anwender auch selber tauschen kann. Die Schaber im Fülltrichter sind aus detektierbarem Material und verliersicher konstruiert. Alle Oberflächen wurden auf die neuen Hygieneanforderungen hin optimiert. Das Resultat dieser konsequenten Konstruktion ist ein modernes und glattflächiges Design bestehend aus hochwertigem Edelstahl.
Einfache Demontage und automatische Reinigung schaffen ideale Bedingungen für geringen Reinigungs- und Pflegeaufwand. Einzigartig ist das integrierte Reinigungssystem im Förderwerk des KK500 (Clean in place). Durch Aktivierung über die Touch Control Steuerung wird das Fördersystem automatisch mit Wasser gereinigt.
FTC1000 Die neue Steuerungsgeneration mit klappbarem kapazitivem Touch-Display
Erstmals vorgestellt auf der IFFA wurde mit dem KK500 die FTC1000. Die mit der FTC1000 ausgestatteten Füllmaschinen enthalten zwei leistungsstarke Dual Core CPU’s bestehend aus HMI (human machine interface) und MC (machine control).
Während die MC die immer schneller und komplexer werdenden Prozessabläufe in der Füllmaschine und in den Vorsatzgeräten organisiert, kümmert sich die HMI neben der Ein- und Ausgabe von Parametern über das Touch Display um die Rezepturen, Datensicherung, diverse Protokolle und Prozessdaten, die sie in die Außenwelt z.B. über die OPC-UA Schnittstelle kommuniziert.
Dies ist im Hinblick auf Industrie 4.0 die leistungsfähigste Lösung, um die hohen Datenströme zu verarbeiten. TC1000 bietet eine Datenschnittstelle nach dem Weihenstephaner Standard für die Betriebsdatenerfassung. Eine File Server Funktion sorgt für eine einfache Möglichkeit Daten und Rezepturen über das Netzwerk bidirektional zwischen PC und Füllmaschine auszutauschen.
Die HMI-CPU hat mit ihrem hochauflösenden 12“ Brilliant Display mit LED Backlight, kapazitivem Multitouch und klarer Grafik einen hohen Wiedererkennungswert. Die durchgehende Frontscheibe aus Polycarbonat ist mit einer austauschbaren Schutzfolie ausgestattet und bietet somit die höchste Schutzart IP69K.
Die MC-CPU ist geschützt im Schaltschrank verbaut und leistet mit ihren lüfterlos gekühlten Prozessoren und verschleißfreien Festplatte sehr gute Arbeit bei der Prozesssteuerung und Automation. Das Datenbackup erfolgt automatisch.
Die optional integrierbare RFID-Technik dient der Autorisierung des Bedien- und Servicepersonals per RFID-Chip und schaltet individuell für jeden Bediener entsprechende Parameterebenen frei.
Perfekte Ergonomie durch das robust gestaltete Klappterminal. Optimale Bedienbarkeit während der Produktion, optimal geschützt während der Reinigung Dank des IP69K-Standards und Hygienic Design.